Ignition Discover Gallery
2024 Firebrand Award Winner
Deloitte
Project For: Goodman Fielder
Food Manufacturer Uses Ignition To Enhance Efficiency & Quality In Three Largest Bakeries
Project Summary:
Goodman Fielder is a food manufacturer with a portfolio of well-known grocery and foodservice brands. Goodman Fielder’s markets span Australia, New Zealand, Fiji and the Islands, Papua New Guinea, and New Caledonia. This project includes the Goodman Fielder Baking division in Australia, starting with their three largest bakeries: Clayton in Melbourne, Victoria; Moorebank in Sydney, New South Wales; Burleigh Heads in Gold Coast, Queensland. Goodman Fielder envisaged streamlining the day-to-day production processes through Digital Transformation and implementing modern Industry 4.0 best practices and technology. To enhance production efficiency and product quality from the mixing equipment, Goodman Fielder identified the need for additional data automation, prompting the establishment of a SAP, Recipe, and Scheduling Initiative.
Problem:
Goodman Fielder Bakeries were facing production challenges stemming from outdated operational data management practices. These practices were hampering the realization of potential efficiencies and product quality improvements.
The daily operations team managed production using a combination of basic HMI interfaces as well as printed Excel sheets, with no integration into other production or business systems. This led to labor-intensive information management, with minimal automation and manual data capture prone to information and decision errors, hindering real-time understanding of operational conditions.
Some quality issues were only evident following the completion of the bread-baking process. Quality loss consumed significant additional processing costs and had a negative green impact to all the sites.
Deloitte identified that the key goals moving forward were:
- Right-first-time dough mixes.
- Reduction in scrap.
- Increase in dough mixer availability.
- The scope included five baking lines across three sites.
Deloitte identified two major issues:
Management of mixing recipes
The recipes governing ingredient addition and mixing parameters were stored and managed directly on the mixing equipment. This practice of “siloing data” led to customized recipes for each mixer, making it inefficient to implement updates and recipe enhancements across all mixers at a site.
Management of mixing schedules
Mixing schedules were communicated to the operations team through a printed SAP information data sheet, which was then manually entered into the mixing equipment. Adjustments throughout the daily production schedule necessitated multiple versions of printed schedules to be distributed to the operations team and subsequently re-entered into the mixing equipment. This cumbersome process introduced errors and restricted the realization of optimal production schedules.
Solution:
The first stages of Goodman Fielder’s digital strategy have been addressed by implementing a modern SCADA/MES platform built with Ignition and Sepasoft MES. The technology has enabled equipment connectivity as well as a rapid application development environment.
Goals for the new system include:
- Provide increased visibility of previous, current, and new batches.
- Allow SAP production plan to be updated dynamically.
- Remove dependence on Excel spreadsheets.
- Create a foundation on which additional best practices can be added such as track and trace, material consumption, etc.
- Develop and implement a recipe control system to ensure the optimized recipe is always applied.
- Increase operating efficiency of production equipment.
- Improve production visibility and transparency.
- Introduce a software platform that provides a solid foundation for future business initiatives through rapid application development and continuous improvement initiatives.
Deloitte recommended a two-staged implementation approach for recipe and schedule management.
The new automation of data from SAP to the factory floor represented a quantum leap in the working method used by the site operations team. Goodman Fielder decided to roll out the recipe system initially. This provided a view of the new system to a smaller audience. The system was used extensively in a short time with immediate positive feedback, allowing the technical baking staff to create, edit, and delete recipes based directly on BOMs pulled from SAP. The recipe parameters were then written to the PLCs. The objective was to create a recipe system that enables production teams to regularly review and adjust production recipes to ensure product consistency and quality.
The recipe system was followed by an interface that processed and sent production instructions-based SAP production schedule to respective workstations.
In parallel with this project, Goodman Fielder also envisaged introducing new automation interfaces where visualization and connectivity were sorely lacking in the process.
Goodman Fielder needed to achieve minimum functional compliance that retained the existing weigh station (used for manual/hand additions) and included viable products required to enact recipe and schedule management. This included:
- BOM SAP interface.
- Production planning SAP interface.
- Creation of recipes based upon SAP BOMs.
- Implement business rules against materials or material types.
- Dynamic use of the SAP-generated production plan. i.e., updates in SAP would be immediate.
- Workflows for abnormal conditions.
- User interface in weigh-ups for operators to view production plan and recipe. The Mettler Toledo RMS (Real-time Microbial Detection System) would be updated manually.
- Connection to Baker Perkins Line PLC to update recipe parameters. Bulk adds + mix. Reports and dashboards to provide visibility on: Previous, current, and future batches. Data for analysis for technical teams.
Results:
The following is a list of some of the improvements that Deloitte has seen as a result of implementing the Ignition MES/SCADA system:
- Improved accessibility to reports with the ability to download data to client PC makes it easier to use data in issue investigations.
- Reports can now be generated using up-to-date real-time data or historical data for comparison of current status to previous status.
- Visualization of plant and factory operating conditions allows ad hoc investigation if issues occur.
- Visualization of plant cycle times identifies potential issues before they occur. Reduction in material variance due to accurate scheduling.
- Downtime and waste reduction due to automated scheduling from ERP to plant equipment.
- Reduction of paperwork — less actual paper used and less time skilled operators are spending copying data from HMI to paper forms.
- Reduction in unaccounted waste.
- Better and more consistent quality of final product due to increased ability to modify product master recipes.
- Tracking/audit trail of process parameters allows for better outcomes from root cause analysis of production issues.
- Improved accessibility to information due to integration of MQTT broker and IIoT devices.
Start Date: May 2022
Deploy Date: Ongoing
Project Scope:
Tags: 13,000 at each site (x3)
Screens: 30 screens at each site (x3)
Clients: 12 at each site (x3)
Alarms: 8,000 at each site (x3)
Devices used: Existing office desktop computers located in the manufacturing areas. Additional tablets are being introduced when a suitable WiFi network is available in the plant.
Architectures used: Enterprise
Databases used: MSSQL server and EAM at Clayton, Moorebank, and Burleigh Heads. SAP Staging Tables — Custom Recipe and Schedule – Sepasoft Alarm DB - Ignition Historian DB - Ignition
Historical data logged: Event data is logged based upon the start or completion of a batch. The majority is logged in either Sepasoft schemas or custom built. Time-series data is logged via Ignition historian. Currently less than 1,000 tags are being logged per site.
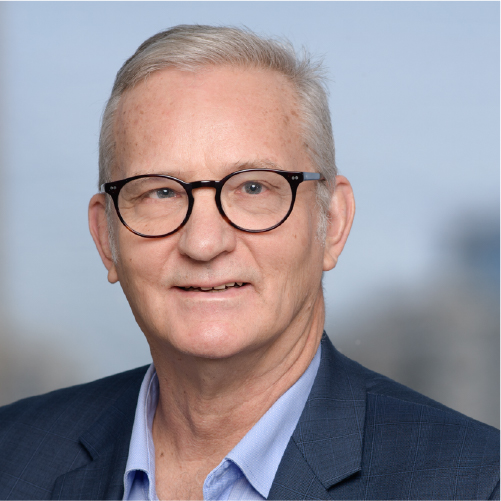
Presented By:
Gordon Cornish
Gordon Cornish is a Principal within Deloitte’s Smart Manufacturing practice in Australia. Gordon has a practical background in automation solutions and over 40 years experience in the automation industry. Gordon has been actively involved in managing the execution of the Goodman Fielder project. David Hermann is responsible for leading the design and scope requirements for Goodman Fielder.
Created By:
Deloitte
Deloitte’s smart manufacturing practice in Australia helps clients transform their operations and uplift production performance by applying the latest in advanced digital technologies. By taking a holistic approach to raising performance by applying people, process and technology transformation, they enable clients to drive increased value within and beyond the four walls of manufacturing, while ensuring that people and processes are part of the successful transformation strategy.
Website: deloitte.com/au/en.html
Project For:
Goodman Fielder
Goodman Fielder is a food manufacturer with a portfolio of well-known Grocery and Foodservice brands. Goodman Fielder markets span Australia, New Zealand, Fiji and the Islands, Papua New Guinea, and New Caledonia.
Website: goodmanfielder.com
Industry:
Food & Beverage