Ignition Discover Gallery
2024 Firebrand Award Winner
IDOM
Project For: Cinfa
Ignition-Based UNS Provides Real-Time Orchestration For Pharmaceutical Company
Project Summary:
The FMS (Factory Management System) is a real-time automation orchestrator for the entire plant, including production equipment, intra-plant logistics, warehouses, utilities and clean rooms. Through the integration with Level 2, 3 and 4 applications, the FMS delivers a layer of abstraction and a single-point-of-access that allows operations to monitor and control all processes in real time. FMS’ abstraction layer is based on the concept of the Unified Namespace where all applications can exchange the required information for process automation in a decoupled architecture and where Cinfa has set the information semantic model of its business.
Problem:
Cinfa was undergoing a major project of a new greenfield plant, called the NEO project, to manufacture pharmaceutical products. The plant was designed with a high level of automation, where all production and logistics operations, including internal material handling and warehousing of raw materials, WIP and finished goods were managed by a plethora of isolated applications.
The problem was that Cinfa needed to create a hub where all applications could interface without changing their native communication protocol, and at the same time could monitor and dispatch messages according to the production plan. The solution envisioned by Cinfa was not a simple communication middleware, but rather an orchestrator of all messages that each step of the production required at specific moments, based on the overall status of the plant.
By the time Cinfa realized that without such an application they could not successfully run their new plant, there was less than a year remaining before the first batch of product was supposed to launch production. Additionally in the pharmaceutical sector, every application, before going live, has to pass a thorough and lengthy validation process.
Solution:
IDOM implemented a solution that now plays a fundamental role in the orchestration of plant operations, acting as a link between previously isolated or disconnected systems and subsystems. The SCADA/MES capabilities of Ignition have made it possible to serve, with a single solution, different needs for both supervision and production management.
IDOM built the overall solution architecture around the following main modules:
- Inbound/Outbound interfaces
- System operations
- Use case development
- User interface
- System alarms and events
- System administration
Operational use cases include:
- Production Process Control: nine use cases, including work order sequencing, clean room conditions to launch production, work order setup procedures, batch dispatching to all plant equipment, access and door control, real-time dashboard of all in-progress production, alarms and notifications.
- Production recipes management: select and dispatch product recipes to equipment.
- Production container management: 12 use cases, from object creation and management, real-time visualization of current location, container cleaning, etc.
- Pallet management: three use cases, including raw material (RM) movement to consumption points in the plant, RM returns to the warehouse, and finished good movements.
- Traceability: two use cases, with full traceability for all raw materials and all WIP.
- Data acquisition: four use cases, including production equipment efficiency, production step progress, machine status and signal historian, production reports for all rooms.
List of interfaces with legacy applications:
- ERP/SAP
- APS/Asporva
- LIMS/STARLIMS
- CMMS/ORMA
- WMS/ULMA automated warehouse (AS/RS)
- AGVs/ABB-ASTI
- RFID/Cima
- BMS/Desigo
- Production process 1/Syntegon
- Production process 2/Fette
- Production process 3/Bosch
- Production process 4/SERVOLiFT
- Clean rooms/Vidmar
- Doors/STE
List of technologies/protocols used for the interfaces:
- WebServices/API REST/IDOCS
- DB connectivity (Oracle 19c)
- OPC UA server/client
- S7 driver
- Modbus TCP
IDOM built a Unified Namespace according to ISA-95 structure. The UNS is structured using UDTs and a specific tag provider named “UNS” created in Ignition to provide the semantic model for all data interchanged in the plant, independently from the connectivity protocol utilized. A total of about 4,000 different messages have been configured to be managed by Ignition during operations.
List of UI developed, using both Perspective and Vision:
- Perspective workstations: 14 UIs to monitor all production processes in the different areas. SCADA functionalities and clean room conditions using tables.
- Vision clients: six UIs to monitor all climate conditions of clean rooms and eight UIs to monitor the different production areas.
Ignition Modules used:
- SQL Bridge
- Perspective
- Vision
- Alarm Notification
- OPC-UA
- Web Dev
Results:
The Ignition solution has delivered the following benefits to Cinfa:
- Real-time visibility of the state of the business, providing elements of supervision of the production process "end-to-end" both to people, through graphical interfaces, and to other systems through the UNS.
- Reduction of human error, integrating the electronic batch record (EBR) with plant equipment. Equipment recipes are automatically transferred, and process values and controls are integrated without the need for manual intervention.
- Reduction and optimization of internal material movements, managing the transfers of pallets and product containers through AGVs between storage points and consumption points.
- Regulatory compliance, immutably recording the details of all production process operations so that the evolution of a batch can be faithfully reconstructed, storing all the transformations from raw materials to the final product throughout the different processes.
As an unexpected or unanticipated benefit, thanks to an exhaustive traceability of production operations, the system has made it possible to analyze the causes of deviations between theoretical and actual production times, which has led to a substantial increase in productivity.
Start Date: September 2022
Deploy Date: September 2023
Project Scope:
Tags: 8,414
Screens: 41
Clients: 38
Alarms: 230
Devices used: 1 Siemens S71500, 1 Modbus TCP, 19 OPC Connections
Architectures used: Standard
Databases used: Oracle
Historical data logged: 9 tags
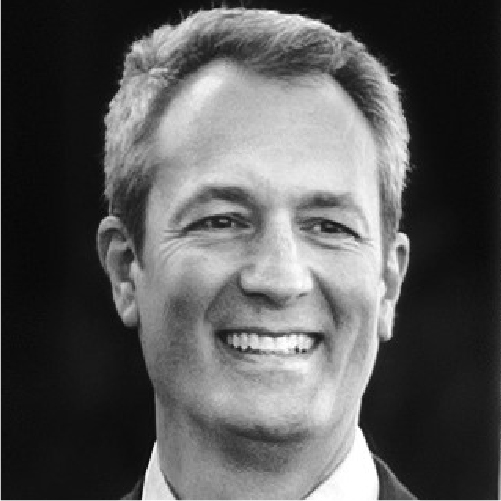
Presented By:
Marco Busatto
Marco Busatto, with more than 25 years of experience in operations management, supply chain and IT/OT software solution implementations, is currently the Director of Industry 4.0. APICS and PMI certified, and holds a BS in Production Automation Engineering from Politecnico of Milan and a MS in Industrial Engineering from the State University of New York. He has extensive experience in several industrial sectors: automotive, food & beverage, steel, electronic packaging, chemical and pharmaceutical.
Created By:
IDOM
IDOM is an independent firm providing consulting, engineering, and architecture professional services. IDOM has carried out complex and challenging projects for more than 65 years in more than 125 countries. IDOM’s differential value is the capacity to integrate multidisciplinary teams that combine complementary perspectives and execute projects in each part of the value chain. IDOM has been ranked first to carry out the Strategies and Roadmap for Industry 4.0 in Spain, among the 43 organizations presented at the national level.
Website: idom.com/en
Project For:
Cinfa
Cinfa is a pharmaceutical company with 100% Spanish capital and 55 years of experience, specializing in the development, manufacture and marketing of medicinal products and health solutions. Its wide range of products and the quality, efficacy and safety of its treatments have enabled Cinfa to position itself as the laboratory with the highest number of dispensations in Spanish pharmacies, thereby making it the one the most present in Spanish households, with an average of ten treatments per household. Cinfa’s solutions are also present in more than 100 countries around the world.
Website: cinfa.com
Industry:
Pharmaceutical