Ignition Discover Gallery
2021 Firebrand Award Winner
BHP
High-Performance HMI and Single User Interface for Minerals Division of Global Resources Leader
This project is a high-performance human-machine interface (HMI) which assists technicians at BHP’s Technology Remote Operations Centre (TROC) for Minerals Australia in monitoring and managing the status of critical technology infrastructure and components across the operations.
BHP has provided visibility and context of PLCs, switches, servers, applications, substations, data centers and more, using its internally developed OPC UA module for OSI PI to bring in hundreds of thousands of data points.
BHP has also integrated with many of its other enterprise platforms to provide quick, intuitive, and easy-to-digest context at a glance to enable TROC technicians.
The BHP HMI solution is a significant innovation that uniquely integrates the IT world into the OT space for the mining industry. BHP has used new technology and modern integration to combine huge volumes of real-time data and context — presenting this in an actionable form to enhance safety and productivity. BHP’s initial research found no solutions in the market that met its needs, so it chose to develop an innovative solution.
PROBLEM:
The TROC operates 24x7 supporting critical technology across assets in Australia. Its purpose is to prevent and minimize safety and production impacts to the assets, triggered by failure or degradation of critical technology. As such, a TROC technician occupies a control desk for a 12-hour shift, monitoring and responding to all issues impacting critical technology services.
A TROC technician must therefore watch, absorb, and interpret large amounts of complex data to determine if any action is required to prevent or mitigate an impact to operations.
Prior to the deployment of HMI, the TROC technicians performed this process manually, by searching through alerts across multiple isolated systems. These alerts were presented in the form of thousands of uncontextualized emails, manual and automated phone calls, or simply through “eyes on glass,” monitoring multiple application screens and logs.
With an ever-increasing reliance on technology to underpin critical safety and production functions across operations, a missed alert or delayed response could result in the shutdown or evacuation of an entire operation, or worse, someone being injured. To avoid this, BHP needed to improve the way TROC was presented with vast amounts of information.
SOLUTION:
After extensive research, reviewing best practices, and interviewing/observing TROC technicians, BHP defined “what good looks like.” This would be TROC technicians receiving ONLY critical data, presented in near-real time, in a way that provides actionable context, displayed on a single pane of glass.
Developing the solution was complex, as BHP’s Australian operations consist of:
- 30+ sites
- 20+ network domains
- Tens of thousands of devices
- Hundreds of thousands of data-monitoring points
For the software backbone of HMI, BHP chose Ignition Perspective. This solution provides the means to present information in a modern browser interface, provides a zero-install environment, is mobile-device-friendly, and allows BHP to present all the information to the TROC technicians in a traditional SCADA environment. Importantly, it allows the team to leverage an off-the-shelf solution with traditional SCADA functionality, alongside modern IoT connectivity options.
The development team has spanned BHP’s Australian assets to collect device health and process data via the existing OSI PI historian infrastructure, collecting and contextualizing 1.1 million data points every few seconds. BHP achieved this by developing its own OPC UA device modules for Ignition. This integrates with the OSI PI data infrastructure using "data pipes" which ingest the internal OSI PI data stream from Interface/Collectors before it is written to disk in each Historian Archive. Through research and development, BHP found that this is the most efficient and scalable way to collect and feed information into the Ignition SCADA platform. Inductive Automation provided excellent guidance and assistance in this development.
This data is automatically mapped back to data models, while bringing in ServiceNow data (via API) on current incidents, problems, and changes, to provide more context in an alarm situation. BHP also hooks into predictive Splunk alerts via API and consolidates this along with all the asset downtime into alarms using Denodo VSQL calls.
BHP has configured for monitoring:
- 800+ servers
- 1,400+ switches
- 79 GE PLCs
- 257 AB PLCs
- Many services and applications
Ignition Perspective allowed BHP to leverage scripting, automation, and modern integration to quickly deploy at scale. Most of the data models built for these devices in Ignition are scripted and automated, so BHP can quickly deploy at scale and provide the ability to refresh when new devices are added or removed from the landscape.
What made this unique is the scale of the scope across Australia, the application of Technology Health Monitoring, the application of ASM and Alarm Management to Technology Monitoring and the data connectivity to OSI PI, along with how much of the solution is scripted or automated in creation.
RESULT:
The system is providing better visibility and context to operational personnel in the field, as well as a better experience when the TROC is contacted, with the TROC technician already aware of the issue and actively resolving it. Usually, issues are being proactively resolved prior to the operations noticing any effect or impact. As the TROC HMI is accessible to all employees, others outside of TROC watch and respond to alarms, preventing issues earlier than in the past.
BHP is working on adding more context into the HMI to provide TROC Technicians with the visibility and quick fault-finding they require. Pages already developed include:
Server Health Monitoring
PLC Health Monitoring (GE and AB)
- Layer 2 physical network layouts
- Layer 3 physical network layouts
- Power distribution overviews (from Power Station to UPS and devices)
- Sub Station and server room overviews
- Application health overviews (Historians, Fleet Management, SCADA)
- Alarm status page side panel drill-in with trend and ServiceNow data
- Specific Material Risk views showing critical equipment health (Ship Line Tension, Chlorine Monitoring)
There is also a cultural benefit, as BHP is providing a solution that is “fit for purpose” for TROC, rather than presenting the team with multiple siloed solutions which do not provide the context required.
The HMI system results in fewer outages and IT failures. Over time, this will result in significant cost savings from disruptions that have been avoided across all of BHP’s operations in Australia — and, if replicated to other operations, potentially globally.
Additional Information:
The team applied international best practices, standards, and learnings from industry in terms of Alarm Management (ISA 18.2), High Performance HMI Design (Abnormal Situation Management) and modern data collection via OPC UA and API Integration to monitor critical technology across Australia in near-real time.
Project Scope:
- Tags: 1.1 million
- Screens: approx. 200
- Clients: approx. 60
- Alarms: 160+ on UDTs, 53k+ instances
- Devices used: 9AF OPC UA Device (Custom), 1 OPC DA
- Architectures used: Redundant
- Databases used: SQL Cluster, Denodo VSQL
- Historical data logged: 53,000+ tags
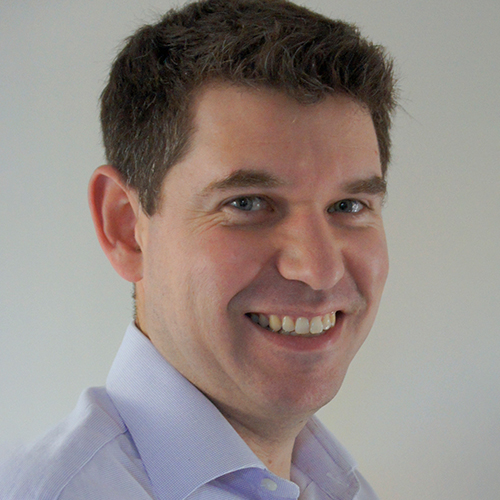
Presented By:
Chad Burrows
Chad is a chemical engineer with more than 16 years of experience working with data and technology in the industrial improvement setting. He has leveraged his understanding of industrial control systems, and the wider data and MES landscape within BHP. Chad was the technical lead for the deployment of the current OSI PI infrastructure across BHP’s WAIO assets, and has leveraged that knowledge in the design and implementation of the HMI system.
Created By:
BHP
BHP is a leading global resources company incorporated in 1885. BHP is among the top producers of major commodities including iron ore, metallurgical coal, copper, and uranium, and has substantial interests in oil, gas and energy coal. BHP’s purpose is to bring people and resources together to build a better world. The company’s strategy is to have the best capabilities, commodities, and assets to create long-term value and high returns. In Australia, BHP operates assets in Western Australia (WAIO), Olympic Dam, Nickel West, Queensland Coal (BMA and BMC) and New South Wales Energy Coal.
Website: bhp.com
Industry:
Mining