Ignition Discover Gallery
2024 Project
Musson Industrial
Project For: Murakami Manufacturing USA
Automotive Parts Manufacturer Replaces Manual Logging With Fully Automated Ignition System
Project Summary:
Murakami’s North American plant produces automotive side-view mirrors, processing plastic into assembled mirrors with included electronics. This project transformed Murakami Injection’s pen-and-paper logging process into a fully Ignition-powered system with automated production, scrap, downtime, and changeover tracking.
Problem:
Murakami’s Injection department was like a time capsule; operators recorded defects as tick marks on a piece of paper, manually printed palette labels using an SSH connection to a terminal server, and Injection department leads had to wrangle with an Access database of molds, parts, and defects.
Three main goals for the project were:
- Eliminate all operator paperwork.
- Track all production information (production, scrap, downtime, and changeover time).
- Push real-time inventory information into Murakami’s ERP system.
Solution:
Musson Industrial designed a database schema in order to build a logical relationship between presses, molds, cavities, parts, and scrap pairs. Perspective’s user interface allowed Murakami’s tooling department to manage all configuration in-house. Due to the fact that each mold had a variable number of cavities and each cavity was a member of multiple scrap groups, the user interface greatly benefited from Perspective’s dynamic capabilities. Connecting Murakami’s ERP system to Ignition aided the mapping of cavities to part numbers: available part numbers could be pulled directly from QAD, providing rigorous validation.
Ignition’s Mitsubishi Driver was used to connect over Ethernet to the 16 Mitsubishi FX3U PLCs installed on each of the 16 presses as a hardware interface. The Mitsubishi Driver allowed communications to be performed in Ignition without the need for a third-party OPC UA server.
A unique tag-driven navigation scheme allowed the left and right sides of the operator HMI to function entirely separately, with isolated authentication, navigation, and touchscreen keyboard capabilities.
Label printing was performed using the third-party software BarTender. Musson Industrial developed a BarTender module for Ignition to allow for configuration of BarTender connections from the inside the Gateway user interface and to expose scripting functions for triggering BarTender integrations. Musson Industrial also built a consolidated print station using Perspective to allow operators to scan Kanban barcodes to print palette labels.
Musson Industrial developed a wholly custom Perspective theme (pyro-mui-joy) alongside this project. The theme is an adaptation of Material UI’s Joy library designed to work with Perspective Style Classes. The custom theme allowed the user interface to be rapidly developed while achieving an attractive and consistent design language. The theme and all the associated tooling have been released under an open-source license here (pyro-mui-joy).
Results:
After the application went live, Murakami’s Injection department eliminated all operator paperwork. The logging of all ~2 million injection molded parts per month became a totally automatic process, with increased production, scrap, and downtime accuracy.
With all the Injection production and changeover information being collected in real-time, Murakami’s managers and team leaders have visibility into the true production capabilities of their department, allowing them to identify reasons for long changeover times, spot recurring defect patterns, and compare capabilities between shifts.
The production and scrap information is continuously submitted into Murakami’s ERP system hourly, ensuring accurate inventory for their just-in-time manufacturing methodology.
Start Date: March 2023
Deploy Date: November 2023
Project Scope:
Tags: 1,375
Screens: 30
Clients: 9 Perspective Workstations for operators, + unlimited Perspective sessions for managers/team leaders
Alarms: 0
Devices used: 16 Mitsubishi FX3U PLCs, 1 Zebra printer
Architectures used: Standard
Databases used: 1 Microsoft SQL Database, 1 Progress OpenEdge Database (QAD ERP)
Historical data logged: 2 million rows per month (45 parts per minute), production totals submitted to ERP hourly
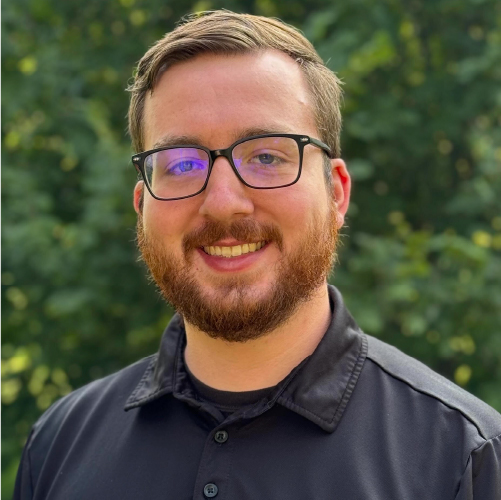
Presented By:
Ben Musson
Ben Musson is a Senior Process Controls Engineer at Musson Industrial. Ben has over 10 years experience designing solutions for the process industries and enjoys leading his cross functional team to produce creative solutions to unsolved problems.
Created By:
Musson Industrial
For over 30 years, Musson Industrial has specialized in tailored process automation systems, blending cutting-edge technology with personalized service. The long-term relationships Musson builds with their clients allow them to provide unique domain specific solutions; they go beyond “out-of-the-box” to anticipate and fulfill evolving needs and deliver innovations that redefine industry standards.
Website: https://mussonindustrial.com
Project For:
Murakami Manufacturing USA
Murakami Manufacturing USA, Inc. is a subsidiary of Murakami Corporation, a 135-year-old global company with headquarters in Shizuoka, Japan. Murakami established their North American operations in Campbellsville, Kentucky in 2000. The facility manufactures exterior rearview mirrors for a variety of automotive manufacturers. The vision of Murakami Manufacturing USA, Inc. is to be a “Supplier of Choice” to their customers and an “Employer of Choice” in the community.
Website: https://www.murakami-usa.com
Industry:
Automotive