Ignition Discover Gallery
2023 Project
Automation Solutions Ecuador
Project For: Uddeholm
Global Collaboration Helps Steel Manufacturer Implement Centralized Control Room
Project Summary:
The main purpose of Uddeholm, a Voestalpine company, is to manufacture high-quality industrial steel tools, applying best practices for an efficient use of resources and a sustainable development. This strategy has led Uddeholm to become the world’s leading steel tool manufacturer with more than 350 years of innovation and presence in more than 90 countries.
To keep fulfilling its purpose, Uddeholm has been developing infrastructure and SCADA projects for its plant located in Hagfors, Sweden. One of these projects was the implementation of a new Heat Treatment Control Room (HTCR). This project aimed to centralize the monitoring and control of all furnaces in the main plant, replace several smaller rooms, increase productivity, optimize performance, and reduce energy and maintenance assurance of long-term growth.
The solution for this project included a scale-out Ignition architecture, Perspective Workstation for visualization, Ignition’s powerful built-in features and ability to be used in a container, and the adoption of a DevOps methodology.
Problem:
Uddeholm had many small control rooms to monitor and control the manufacturing processes of different furnaces which heat the steel to manufacture tools. Most of the furnaces were isolated entities mainly monitored and controlled by a local HMI requiring high-cost maintenance and lacking traceability data to make decisions to improve efficiency.
Solution:
Ignition was already being used at the Uddeholm plant. There were 2 stand-alone Ignition gateways running more than 30 projects and 20 database connections between both gateways. They used a database instance for every gateway, each with a different server.
To implement the Heat Treatment Control Room project, it was necessary to standardize how Ignition would be used. First, the Uddeholm plant implemented a scale-out Ignition architecture to maximize the benefits of using one gateway as a backend to connect with field devices and the other gateway as a frontend to run clients and sessions. Also, the database was centralized in just one server. To accomplish the scale-out architecture, it was necessary to migrate projects with their resources from one gateway to another, move device and database connections to the proper gateway, centralize a local user source, use remote tag providers, configure both gateways using best practices, and migrate the data from the different databases to one server. With this solution, the load was distributed between both gateways, improving performance and requiring just one centralized server for the database instead of two.
The new HTRC required two workstations with five monitors each. Three monitors displayed Ignition process screens. The first screen displayed an overview of furnaces by area with the possibility to select the furnace and provide more detail on the second and third screens. The second screen displayed the graphic representation of the selected furnace with temperature information, the monitor and control of the program (recipe) to use, and information from MES. The third screen displayed trends and alarms of the selected furnace. The other two monitors would display MES programs to run and the XProtect video software to view the furnace selected on camera.
Perspective Workstation was implemented to leverage multi-monitor functionality. One interesting aspect of the project was that the three screens would display the same page at all times, with only the information displayed in the page changing according to the area selected for Screen One and the furnace selected for Screen Two and Three. To accomplish this feature, session custom properties were used to write the number of areas and the number of furnaces, and the view would change the path and the parameter to display the correct area and furnace. Moreover, a feature was created on the navigation bar to assign the area and the operators to work on every workstation. So Workstation One and Two only displays the areas selected. Additionally, an OPC UA connection was made with XProtect Milestone software. The selected furnace was written on a tag for XProtect software that runs an event and displays the camera with the furnace selected on it.
The system monitors and controls more than 40 furnaces, each one with more than 100 tags, so UDTs were created to manage almost 10 different furnace types, standardizing the name of the tags and creating a structure that can fit in dynamic views. Also, named queries were used to have traceability when a furnace program has been started and finished.
Lastly, Uddeholm and Automation Solutions Ecuador worked as a team to bring the HTCR project to life. This could have not been done without using Ignition and the collaborative development feature. For that, the team created a Docker Linux container inside the Uddeholm corporation to allow for ASE’s concurrent development, reducing the time of implementation and associated costs. To apply the deployment best practices, GitLab source was implemented using a DevOps methodology and delivering many benefits to the implementation. A list of issues was created on GitLab to see real-time progress, time invested on every task, track project changes, run deployment tests before implementing new features into the production environment, all of which reduced errors and saved time during implementation.
Results:
For Uddeholm, the implementation of the HTCR project allowed operators to work together in the same room, making it easier to coordinate activities. It also reduced physical space, centralized the monitoring of the furnaces process, centralized data, increased the traceability of furnaces operation, saved money by using one less server, optimized performance, and reduced energy and maintenance.
Using containers and GitLab during deployment and development made the collaborative implementation easier, quicker, and more efficient, diminishing errors on production and having better control of changes during the process. It also lowered the cost of implementation.
The HTCR project also allowed for the implementation of new features such as an overview window with the real distribution of the furnaces and core information of the process for informative purposes. An application in Perspective now connects with energy API Nordpool to gather information on energy expenditures and cost. This feature will be used this year to maximize the furnaces efficiency and decrease the use of excess energy. Another application was developed to emulate a connector to a Kafka open-source-as-consumer to gather the data that will be used later this year.
The HTCR project made a difference in the Uddeholm plant. Having a centralized control room with centralized data made it possible to standardize furnace operation. Collaborative implementation demonstrated that an application could be developed and deployed remotely between one team in Sweden and the other in Ecuador. The HTCR project laid the groundwork for future projects using Ignition thanks to the confidence it provided both Uddeholm and ASE.
Deploy Date: May 2022
Project Scope:
Tags: 500
Screens: 5
Clients: 10
Alarms: 50
Devices used: 50 - PLC Siemens/OPC UA
Architectures used: Scale-Out
Databases used: 1 SQL Server
Historical data logged: 400
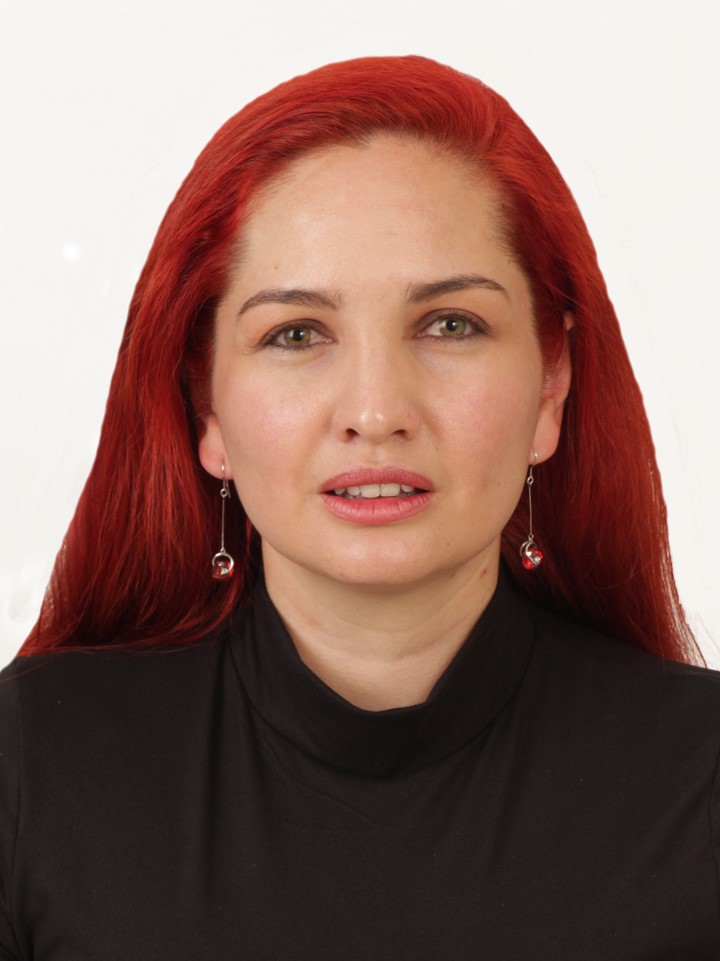
Presented By:
Evelyn Granizo
Evelyn Granizo is an electronic engineer with 12 years of experience in control system integration over multiple industries. Her expertise include logic controller programming, HMI and SCADA design and development, MES system development, database management, third-party system integration, project management, and training.
Created By:
Automation Solutions Ecuador
Automation Solutions Ecuador is the leading control system integrator in Ecuadorian industry with 20 years of experience in implementing control systems. It provides hardware and software, technical training, as well as designing, building, programming, and start-up of information, monitor, control, and MES systems using the best technology and human resources.
Website: asecuador.com/en
Project For:
Uddeholm
Uddeholm is the world’s leading manufacturer of tool steel for industrial tools. Its experience dates to 1640, providing the best high-quality steel tools. Uddeholm has the technology, know-how, product development, and also the passion to assure that every piece of steel and every step of the process, from raw material to finished product has followed the best production techniques. uddeholm.com
Industry:
Manufacturing