Ignition Discover Gallery
2020 Firebrand Award Winner
Flexware Innovation
Project For: Veoneer
New SCADA/MES For Supplier to Leading Automakers
At Veoneer’s facility in Goleta, California, the company manufactures advanced night-vision systems for the world’s leading automakers. For supervisory control and traceability, Veoneer used an internally built system in Goleta. Due to a change in the corporation’s structure, this solution was no longer viable and Flexware was asked to develop a solution that replaced and enhanced the previous solution’s functionality with the Ignition platform. Prior to this engagement, Flexware developed a custom MES solution for a different Veoneer facility with the Ignition platform, and word traveled around the organization about how powerful the software is. It was an easy decision to continue the use of Ignition at the Goleta facility.
PROBLEM:
The system Veoneer had used as both a SCADA and MES solution was no longer available in Goleta. When Veoneer approached Flexware, it explained the breadth of features in its current system as well as pain points and things it hoped could be improved. Due to licensing restrictions of the current system, Flexware had to recreate the functionality of the existing system in only three calendar months.
SOLUTION:
Flexware began by leveraging its internal MES framework, which was built up through various MES solutions developed in the past. This framework includes a database schema, configuration application, and many workstation applications that handle most of the features required in a typical MES solution.
However, the framework had not previously been leveraged for low-level SCADA operations. At Veoneer’s Goleta facility, the previous solution was very tightly coupled with the automation layer and was essential for the line to operate. To add this functionality, Flexware added another layer to its existing traceability architecture, which included products, product routes, product operations, order routes, order operations, and order operation attributes. This layer is called action scripting. Action scripts are routes under the hood and allow Flexware to define low-level PLC interface data transfers and validations inside of its configuration application. Flexware also added a new operation type, HTTP operation, which interacted with line-side PC stations using HTTP GET and POST methods via the Web Development Module.
Flexware developed a complete MES framework from scratch using out-of-the-box Ignition tools. This repeatable framework handles product traceability, inventory management and production run management in addition to other offshoots for production. At the core of the framework, Flexware focused a lot of development attention to build a completely configurable solution that Veoneer can administer entirely from the client without backend modifications.
RESULTS:
This project was very successful. In just three months, Flexware was able to redevelop a system that was built over many years by a large team. The system is now fully implemented and much faster than the previous system.
The biggest improvements the solution provides over the previous system for Veoneer are configurability and data analysis. The previous system was a global system that was used very broadly across the organization. Due to the architecture of the solution, if a new type of action was needed for a particular line process, it would have to be custom-developed and pushed to all instances of the solution globally. The list of requests for new actions was always very large and it could take many months for a request to be completed. Leveraging Flexware’s newly developed Action Scripts, Veoneer can create and customize actions all from the configuration application. This will allow it to be much more adaptive in the future.
Project Scope:
- Tags: 1,000
- Screens: approx. 125
- Clients: 10
- Alarms: 0
- Devices: Kepware (10-15), Allen Bradley and Omron
- Architecture: Standard
- Databases: 3 MSSQL (2 for production, 1 for ERP)
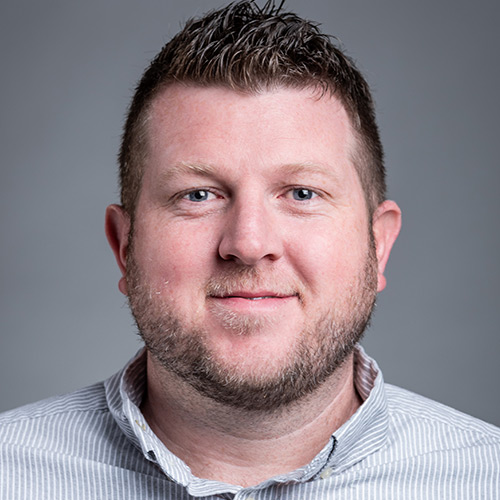
Presented By:
Brian McClain
Brian is the Ignition Team Manager at Flexware Innovation, where he manages a team that develops well-rounded, complex MES solutions such as OEE and product traceability, with some of the world’s largest life-sciences, food & beverage, and automotive companies. On a day-to-day basis, Brian balances business development activities, solutions architecting, and managing the Ignition delivery team, which is a growing team solely focused on Ignition solutions.
Created By:
Flexware Innovation
Founded in 1996, Flexware works with customers to leverage technology to solve real business problems by providing best-in-class software development, automation engineering, manufacturing systems integration, business intelligence solutions, Internet of Things devices and specialized product development.
Website: flexwareinnovation.com
Project For:
Veoneer
Veoneer is a global leader in vehicle technology. The company manufactures and designs industry-leading software and hardware systems for the automotive industry. Veoneer has 7,600 employees across the globe developing cutting-edge technologies in vision, radar, lidar, thermal sensing, electronic controls, and human-machine interfaces. Veoneer develops these technologies in hopes of preventing traffic accidents or mitigating the effects of those accidents that are unavoidable. The Veoneer facility in Goleta, California, manufactures advanced night-vision systems for the world's leading automotive producers.
Industry:
Automotive