Ignition Discover Gallery
2020 Project
APCO
Project For: Ashley Valley Water Reclamation Facility
Perspective Exceeds Expectations for Water Facility
APCO provided PLC, HMI, and telemetry upgrades for the Ashley Valley Water Reclamation Facility (AVWRF). The new HMI was built entirely on the Ignition Perspective platform. The HMI implementation included high-performance, mobile-friendly graphics that gave plant personnel the information they needed to do their jobs.
PROBLEM:
Before the upgrade, AVWRF was using FactoryTalk View SE HMI software. There were changes they wanted to see in the new HMI, and as APCO guided them through a software selection process, they felt that Ignition would most effectively meet their needs. They were particularly interested in the implementation of high-performance graphics that focused on contextualized data and design schemes that improved operator responses to process changes. In their previous system, it was often difficult for operators to key in on operational issues.
Plant staff had previously struggled interfacing many tags in their previous SCADA system. The system had limited trending abilities and no reporting abilities; all reports had to be done by hand daily by an operator then monthly by a manager. Finally, there were no remote connection abilities in the old system, so all on-call events had to be addressed in person, and SCADA programming had to be done on-site.
SOLUTION:
APCO based the design of this system on the key characteristics of Ignition itself. The SQL-based data management guided the approach to developing lab and reporting screens, leading to interfaces that streamlined the data recording and synthesis process. The HTML5 foundation of Perspective led APCO to develop screens that, when scaled from a desktop screen to a phone or tablet, retained functionality and usability.
AVWRF had previously used PanelView touchscreens on their control panels as an option for local control, but with the mobile-friendly nature of Perspective, APCO replaced the PanelView screens with iPads in industrially rated cases. They were mounted on magnetic, wirelessly-charging mounts on the front of the panels where the previous touchscreens had been. This provided the same local control options with the added flexibility for the operators to take an iPad to a location where they needed to work. Additionally, the Plant Manager received an iPad for monitoring the plant remotely, and iPads were provided for use by operators on call. A unique remote access solution was devised using a Secure Remote Connect device that ensured constant, secure access for the plant iPads. The device also has time-limited permission features that ensure remote access pathways are not accidentally left open after remote maintenance is performed.
The Python scripting options in Ignition allowed APCO to implement custom solutions and develop full-featured components that were not otherwise available at the time of development. One such solution was the development of a maintenance mode for individual tags. When a tag is placed into maintenance mode, the tag type changes from OPC to memory, holding the last good value and ensuring that bad data from calibration or maintenance is not historized. As a safety precaution, any tag placed in maintenance mode generates an alarm until the tag is placed back into normal mode. Many other features such as this were made possible by the Ignition scripting options.
RESULTS:
The project was a great success for APCO and AVWRF by every measure. The project came in 17% under budget, even after adding features and components that were entirely developed by APCO, purpose-built to meet plant needs. APCO worked closely with Inductive Automation throughout the development process because the Perspective Module was so new at the time. APCO began development on version 8.03, and by the end of development was working with version 8.07. APCO ultimately developed a custom component library for Perspective, and its use of Ignition templating features led to the development of a flexible, easily upgradable system.
APCO developed a set of lab reporting screens for the operators to input lab testing data. This produced a better method of tracking data input and created the opportunity to observe historical trends in the manually entered data. A report generator was included in the project that pulled historized PLC data and manually entered lab data to generate the reports that had previously consumed so much of the plant manager’s time.
The implementation of high-performance graphics provided operators the ability to respond more effectively to process events. The template-based nature of the graphics made them easily upgradable and changeable according to their future needs. For example, the entire color scheme for the SCADA system can be changed in one location (colors for running, stopped, manual, auto, etc.), a task that would have taken hours on a similarly sized system on a different HMI software. Changes to popups, graphics, and other interfaces are similarly easy.
APCO developed a trending feature built on the Perspective trending component that provided the plant with quick access to pre-built trends as well as the ability to build trends on the go and download the viewed data to a comma-delimited file. The trending interface was built for use on a desktop interface, but subsequently optimized and updated for use on tablets and phones.
“APCO has been great to work with,” said Dean Gibbs, plant manager for AVWRF. “They have taken our ideas and put them into our new HMI software. We now have greater control over our alarm levels, analog devices, VFDs, Power Analysis and also improved several of our PID controls. APCO has also added auto- and self-generating reports by pulling data from the operator input database along with the SCADA database. These reports will make us much more efficient when creating and submitting our monthly and yearly reports to the State of Utah and the EPA. APCO has also created a very secure and unique offsite access for operations and management to view, control, and make necessary changes when away from the facility. This will save us greatly on call-out time and mileage, along with the capability of sitting down with engineers or board members to look at trends, lab results, equipment efficiency, etc., while being off-site.”
Project Scope:
- Tags: 10,478
- Screens: 20 main screens, 43 popups
- Clients: 13
- Alarms: 1,451
- Devices used: 16 (Modbus PQM and Allen-Bradley PLCs)
- Architecture: Standard
- Databases: 2 (MSSQL)
- Historical data logged: 788
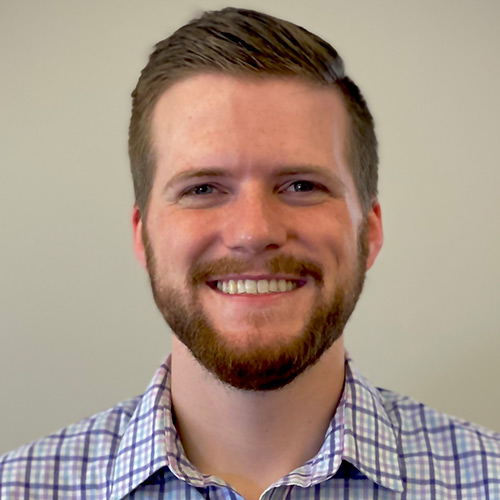
Presented By:
Cameron Price
Cameron has worked at APCO for two years. In his current role as a Control Engineer, he has worked on a variety of SCADA projects, including doing significant work in Ignition Perspective as an Ignition Gold-Certified developer. His chemical engineering education lends a strong process understanding to the work he does, strengthening the quality and robustness of his SCADA programming.
Created By:
APCO, Inc.
APCO is a process control and optimization company that does work across several industries including water and wastewater, oil and gas, manufacturing, food production, chemicals, and mining. APCO specializes in designing and integrating state-of-the-art control systems for the applications of its customers. The company’s goal is to provide the best return on investment for its clients.
Website: www.apco-inc.com
Project For:
Ashley Valley Water Reclamation Facility
The Ashley Valley Water Reclamation Facility (located near Vernal, Utah) discharges into Ashley Creek, and was designed to achieve water quality standards required for the protection of the environmentally sensitive water habitat. The treatment process utilized for the regional facility is an activated sludge/extended aeration process. Disinfection is accomplished through the use of ultraviolet light, thus eliminating the need for chlorine, which could have a detrimental impact on the endangered species in Ashley Creek and the Green River.
Industry:
Water/Wastewater