Ignition Discover Gallery
2018 Project
Piedmont Automation
Project For: Freightliner Trucks
Real-Time and Historical Data Improve OEE
Daimler Trucks North America (DTNA) contracted Piedmont Automation to build a monitoring & control system that would enable DTNA’s operators to call for help and still keep the continuous assembly lines running. Additionally, DTNA required data logging that would identify potential problem areas and provide critical production metrics that would help the company improve its overall efficiency.
Problem:
DTNA’s North Carolina manufacturing facility has several production lines that stretch out over a 1500-foot, in-line assembly process along with many parallel operations. The production lines are composed of more than 125 manual assembly workstations that had no monitoring, control, or feedback of production statuses from station to station. This lack of visualization contributed to substantial downtime and failed to provide the most basic tools to enable maintenance personnel to address specific downtime issues.
Solution:
Piedmont’s charge was to provide an ANDON notification system. ANDON is a manufacturing term referring to a system that notifies management, maintenance, and other workers of quality or process problems. The centerpiece of an ANDON system is local visualization with signal lights and horns to indicate which workstation has a problem. Additionally, the solution provided visualization oversight, controlled operations and equipment interfaces, offered notification to reacting personnel, and logged and reported downtime events.
Piedmont Automation chose Ignition SCADA for visualization and Sepasoft MES software for OEE downtime metrics. Ignition provided the necessary tools for local and oversight visualization of ANDON conditions and production TAKT times for pacing operations. Hundreds of production personnel took advantage of Ignition’s unlimited licensing model, allowing them to view the manufacturing process through the use of strategically located overhead monitors and individual production workstations.
Result:
This interactive ANDON system paced the operators and gave them the ability to notify and call for help. The problem areas were displayed in real time and broadcasted to the entire 1500-foot assembly line, showed where the problem area was located, what type of problem was being experienced, and how it affected various other stations. Additionally, equipment interlocks were detected and displayed in a similar fashion, and specific notifications went out to maintenance. This visualization allowed operations to react to real-time problems in a real-time fashion, minimizing downtime and increasing efficiency.
Sepasoft MES software provided OEE calculations and an indication of the current efficiency of the assembly lines. Downtime tracking provided information about where and how to make improvements that allowed DTNA to raise its OEE rates. Once implemented, the OEE calculations and downtime tracking gave production managers the tools to measure efficiency and show how to boost efficiency rates. These tools included downtime reports by shift, by line, by station, by downtime type, and by equipment. These reports identified issues with the production process, with personnel, and with equipment.
Prior to implementation, DTNA was at the mercy of its technicians’ troubleshooting skills to locate and diagnose equipment and operator errors that often paralyzed the production lines. After implementation, Ignition provided a real-time view of production for immediate solutions to downtime events, and Sepasoft MES OEE software provided an historical view for strategic production improvements. This brought the available rates and production rates closer together for a better overall equipment efficiency performance.
Project Scope:
- 50,000 tags
- 50 screens
- 100 clients
- 1,000 alarms
- 40 Logix PLCs
- Standard Ignition Architecture
- MSSQL and MySQL databases
- 150 OEE cells
- 4,000 OEE tags
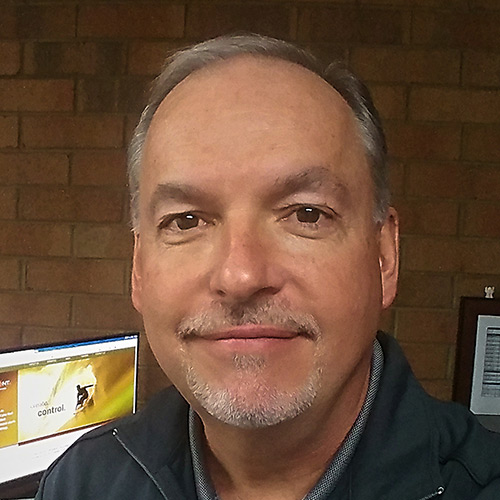
Presented By:
Bob Worth
Bob Worth co-founded Piedmont Automation in 1999 and his company is located in Winston-Salem, N.C. Bob has a BS in Electrical Engineering and has worked for companies like Raytheon Engineering and RJR Nabisco as a Controls Engineer and is primarily responsible for sales, marketing, and the overall strategic direction of the company.
Created By:
Piedmont Automation
Piedmont Automation was established in 1999 and is celebrating its 20th year in business as a systems integration company serving process manufacturing, discrete manufacturing, food, tobacco, water and wastewater, and many other industries. Piedmont has provided world-class automation solutions in areas of process control, material handling, SCADA & OEE productivity tools, Andon systems, KPI dashboards, data collection and reporting, remote telemetry systems, instrumentation and controls, and UL panel building. The company’s talented and experienced technical staff has built a reputation delivering innovative and reliable solutions domestically and internationally. This is done using leading-edge technologies to develop automation solutions in some of the most demanding manufacturing environments imaginable. As automation specialists, Piedmont is constantly evaluating new technology products and looking for ways to use them to customers’ advantage. This is why Piedmont Automation started using Inductive Automation products in 2010 and became a Premier Integrator deploying Ignition SCADA & OEE solutions in many of these industries.
Websites: www.TeamPiedmont.com
Project For:
Freightliner Trucks
Freightliner, or Daimler Trucks North America (DTNA), began in the late 1930s as Consolidated Freightways Trucking Company in Salt Lake City, Utah. After WWII, the company changed its name to Freightliner and moved to Portland, Ore. in the 1940s, and was eventually acquired by Daimler-Benz in 1981. For more than 70 years DTNA has been producing brands like Freightliner & Western Star Trucks, Thomas Built Buses, Freightliner Custom Chassis Vans, and Detroit Diesel engines. DTNA is the leading commercial vehicle manufacturer in North America. As Daimler Trucks North America enters its eighth decade, it remains committed to the values on which it was founded: innovation, quality, and an unwavering dedication to meeting customers’ needs.
Industry:
Automotive